Customer satisfaction surveys should be clear, concise, and targeted.
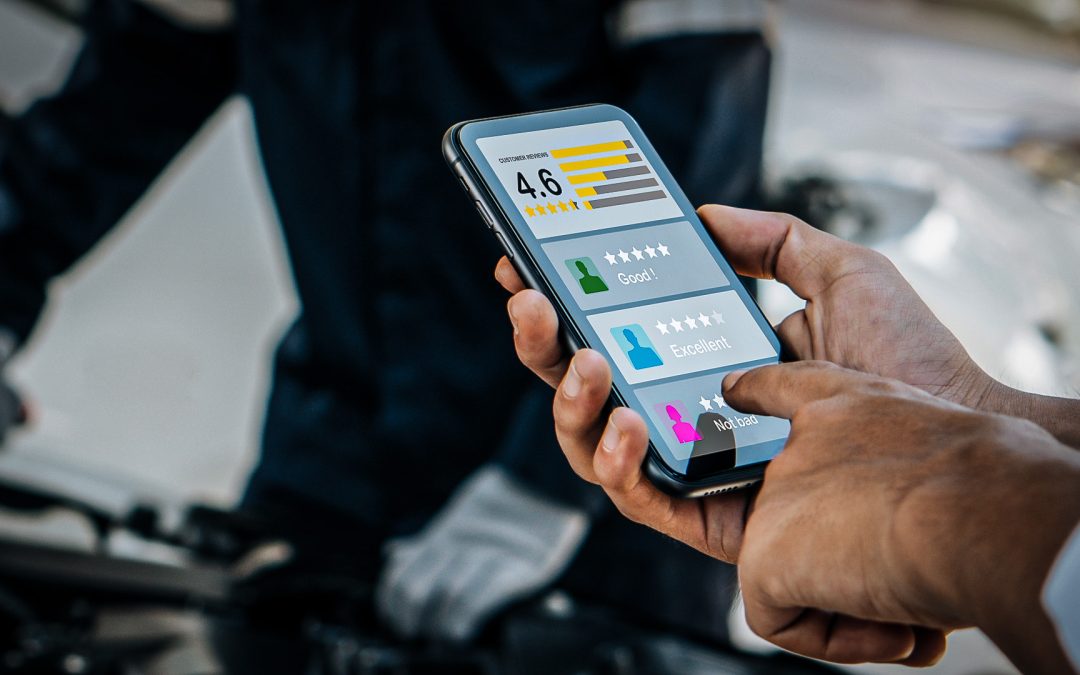
PWM (pulse width modulation) is used to control all sorts of things on the modern vehicle. Its use has proliferated to lighting. Here are a few reasons why.
You’ve seen it, no doubt. Some cars have eyebrow-raising charging strategies with big voltage spikes, but even on “normal” charging systems, charging voltages keep sneaking up. Vehicles have huge electrical draws and the systems that deliver that juice reliably have components like AGM batteries that can take a charge faster than their lead-acid counterparts.
The headlights don’t take kindly to that, though. Halogen headlamps will indeed burn brighter at higher voltage, but they put off a ton of heat doing it, which wastes precious electricity. Further, as anyone who’s overdriven a halogen bulb can tell you, the price for that additional brightness is a massive decrease in lifespan.
Pulsing the DC current powering them regains some life, saves electrical load, reduces heat, and the penalty is almost nil. Halogen lamps have relatively long rise and decay time. Lighting designers can exploit this characteristic to their advantage because it helps “smooth” the effect of pulsed current to the observer.
Photo: Mike Apice.
I’m about to speak in some massive generalities regarding how people perceive brightness. With that caveat in place, driving LEDs with a pulsed (rather than constant) current can make LED bulbs appear brighter. Since the voltage applied to an LED can be increased if the duty cycle is reduced, the light appears brighter, so long as the cycling rate is kept above what the human eye can perceive.
The ability to quickly modulate pulse width allows for lights to exhibit a range of intensity.
Even on cars that utilize good ol’ incandescents on the caboose, the second filament in many multifunction stop/turn/tail bulbs can be eliminated. The advantage here is twofold: first, the rise time from “taillamp” intensity to “brake light” intensity is shortened, because the filament is already heated up and running. It also theoretically leads to longer bulb life, since the temperature of the filament isn’t swinging as wide so often. The downside to this, of course, is that if a bulb filament dies, all functions (stop and tail) are lost.
Interestingly, you might also see PWM used to create LED lights that mimic the behavior of incandescents. The difference in rise and fall time between LEDs and incandescent bulbs is certainly noticeable, so much so that the rapid blink of an LED is usually known as “hard blinking.” PWM-controlled turn signals display the ability to “soft blink,” or in the case of Mazda, “Dimming Turn Signals.”
I’m not sure I take lighting as seriously as Mazda Designer and Lamp Development Leader Atsushi Yoshida does in that article—but I appreciate his work. I recall seeing these when they arrived on the scene and thinking it was a pretty nifty detail most people would overlook.
If a blockhead like me noticed it, others probably do, too.
One way that happens is with DRLs, an automotive feature Shop Press has covered in the past. Rather than having a separate set of daytime running lamps, which has been done before, some automakers have chosen to use high beam bulbs as DRLs by modulating them.
Or this strategy allows the automakers to save some money if you’re a cynic. I don’t think I am surprising anyone when I mention that automakers are always looking for ways to cut costs. While America doesn’t mandate the use of daytime running lamps, some countries do. By controlling the feature through software instead of adding hardware, automakers enjoy the luxury of reduced hardware costs and greater economies of scale when purchasing parts.
And of course that bit about the dual-filament bulbs being displaced factors in here, too. Instead of having dual-intensity bulbs or multiple bulbs for multiple intensities, a single filament can stand in where a dual might have once been used. Every cost like this that is reduced or eliminated adds up to lots of money when applied across millions of vehicles produced.
Automotive lighting electrical components have advanced exponentially from the simple systems of yesteryear. Arming yourself with knowledge on how they operate—and how they should be expected to operate—is table stakes for anyone looking to repair, upgrade, or modify the systems.
The articles and other content contained on this site may contain links to third party websites. By clicking them, you consent to Dorman’s Website Use Agreement.
Participation in this forum is subject to Dorman’s Website Terms & Conditions. Please read our Comment Policy before commenting.