Four proven ways to run a tighter ship at your shop.
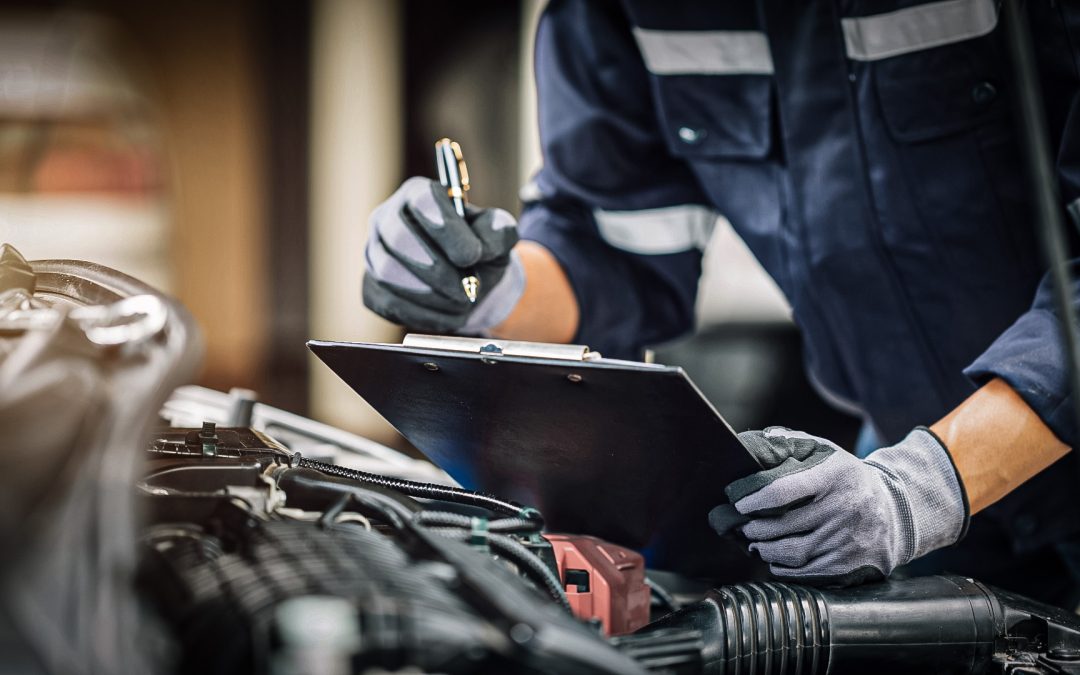
Lubricating O-rings is certainly something I expect you all do. This makes installation easier and also non-destructive—dry metal catching an O-ring can kick off a leak moments after it’s installed. Nothing here is news to you, I am sure. Lubricating with the sealing substance is always a safe bet.
However, when confronted with a O-ring that is oriented vertically when in service, grease is the bee’s knees. The high surface tension of the grease is almost always enough to hold the ring in its groove without falling to the floor, allowing you to line up parts, start fasteners, and generally avoid fighting with the sealing item.
Do your homework on the O-ring material, of course. It may be that you need a silicone grease or something with a more exotic base than the dinosaur goop, but as long as the materials are compatible, grease serves as both an adhesive and a lubricant in this role. I’ve had especially good luck adding a dab of silicone-based grease on long, finicky water pump seals.
I kind of hate RTV silicone. I find it in places it doesn’t belong, it makes a mess, and most people are sloppy at applying it. But I do understand the temptation to grab it when gasketing something since it acts as a mild adhesive.
In a perfect world, most gaskets would be installed dry as the manufacturer often recommends. However, we all know a gasket that won’t lay flat or one that wants to fall usually gets a schmutz of something to hold it in place while we work. Especially when dealing with gaskets that seal oil, I prefer to eschew the RTV and use a dab or two of grease to hold things in place instead. Once oil hits it and washes it away, there is no goop or residue left like RTV can leave behind. (And no matter the color, RTV silicone is ugly.)
Car grease has more uses than you think.
A bit of grease can make capturing swarf from tapping a hole much simpler. Sometimes the chips from a thread-cutting operation might cause damage to the threads that have just been cut. In this case, some grease can help trap chips. A little in the flutes of your tap can be a lifesaver in a blind hole, especially if you don’t have a proper chip-clearing tap.
If you have ever had occasion to have your fingers in a valve body, you know those little check balls roll wherever they like. A little dollop of grease is all it takes to keep them where you need them while you assemble.
I’ve used grease to hold small springs in place before, and it’s a godsend any time you happen to be working on older equipment with loose roller or needle bearings. Similarly, when I’ve had to fire a fastener into a blind hole while fighting gravity, a little bit of grease in the end of a socket usually hangs onto the fastener for long enough to get it started. Unlike adhesive (or RTV, which is admittedly tackier than most grease), it cleans up after installation with a quick spritz of your favorite solvent.
No matter if it’s a dab or a dollop, a squirt or a smear, sometimes a fingerful of grease is just the ticket.
The articles and other content contained on this site may contain links to third party websites. By clicking them, you consent to Dorman’s Website Use Agreement.
Participation in this forum is subject to Dorman’s Website Terms & Conditions. Please read our Comment Policy before commenting.