Four proven ways to run a tighter ship at your shop.
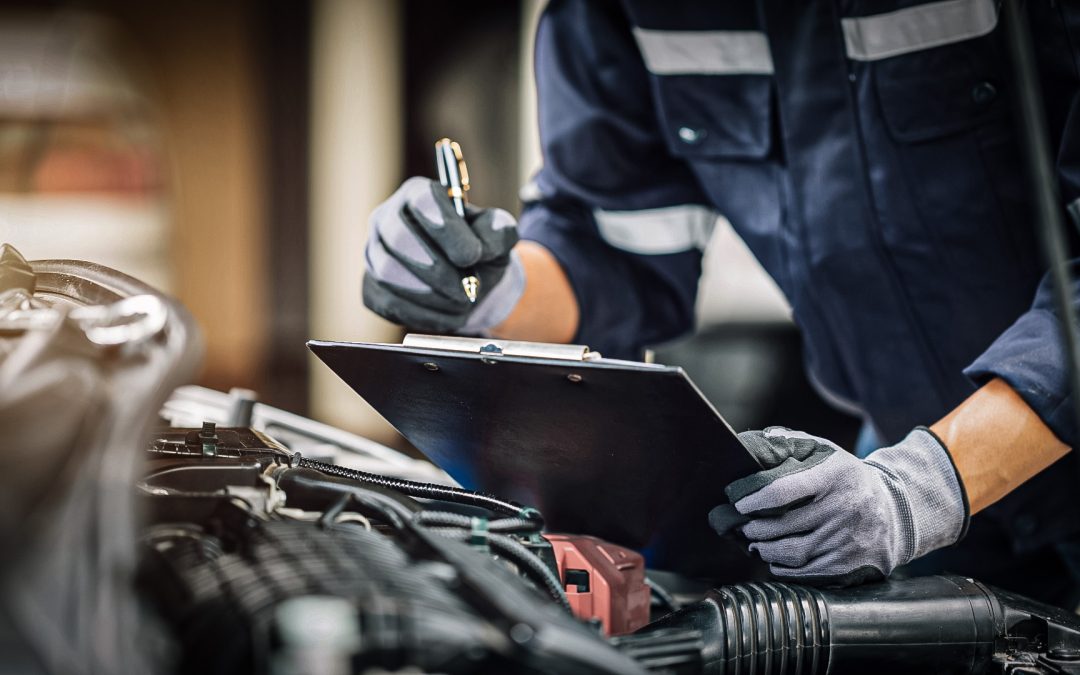
In today’s SHOS, I’d like to discuss captive chassis bolts. You’ll find these holding things like subframes and control arms to unibody chassis, and probably in some other spots, too. In this article, I’m showing the way Dodge chose to mount the first-gen Dakota cabs to the frame because I have them handy, but you’ll find this method of retention oh…pretty much all over the place. I’ve seen Kias and Nissans and Mistubishis and Hyundais all use this method of securing stuff to a unibody vehicle.
Most of us have dealt with this situation before. Effectively, an item is fastened into what is normally a blind hole. Because sheet metal can’t be easily threaded, a captive nut is welded in place to receive the bolt. Another common riff on this is having a threaded receptacle “captured” in place using a sheet metal cage that’s been spot welded to the body.
Here I’ve pulled the interior, cut intp the body, and found the offending item, a cage nut that’s broken its spot welds. Argh. Photo by Lemmy.
After rust and time take their toll, some future service occurs requiring the removal of that bolt, and then all hell breaks loose. The spot welds may rip or the sheet metal cage deforms, and now the bolt just spins. Impact tools can often contribute to “the dreaded spins.”
Before we continue, I must say: look, I understand how we got here. This method of retaining things is inexpensive and light, and it prioritizes speed of assembly in the factory. Most of these parts will never need to be removed within the warranty period, and if they do, the fasteners will probably pop right out.
…and here you can see what lies beneath that cage. Because there was no easy way to grab this fastener, I wound up torching the bolt in half and then using new hardware. I tacked the body patch in, because…well, because someone else will have to get back in here to fix this again, and it might even be me! Photo by Lemmy.
But the hole is BLIND; we can’t easily get to it. The stakes are somewhat high. Accessing the busted area almost always includes cutting out some sheet metal to either weld the fastener in place or to grab a hold of the thing to remove the bolt. (I’m sure that’s not approved in a dealership scenario, but sometimes the wrong way is the right way.) In the case of that Dakota, you can see what had to happen. What should have been a routine “drop one bolt and replace the mounts” job turned into a nightmare involving cutting, fabricating a patch, and re-welding once the job of replacing the busted mount was complete.
Body plugs? Better fastener retainers? I have no idea what the answer is. I doubt any OEM is seriously going to try to fix this issue just because it causes pain to the poor mechanic fixing something a dozen years after a car rolled off the line. But it still stinks and I groan a little when I feel one of these bolt heads suddenly spin free.
I’m betting you do, too.
The articles and other content contained on this site may contain links to third party websites. By clicking them, you consent to Dorman’s Website Use Agreement.
Participation in this forum is subject to Dorman’s Website Terms & Conditions. Please read our Comment Policy before commenting.