Four proven ways to run a tighter ship at your shop.
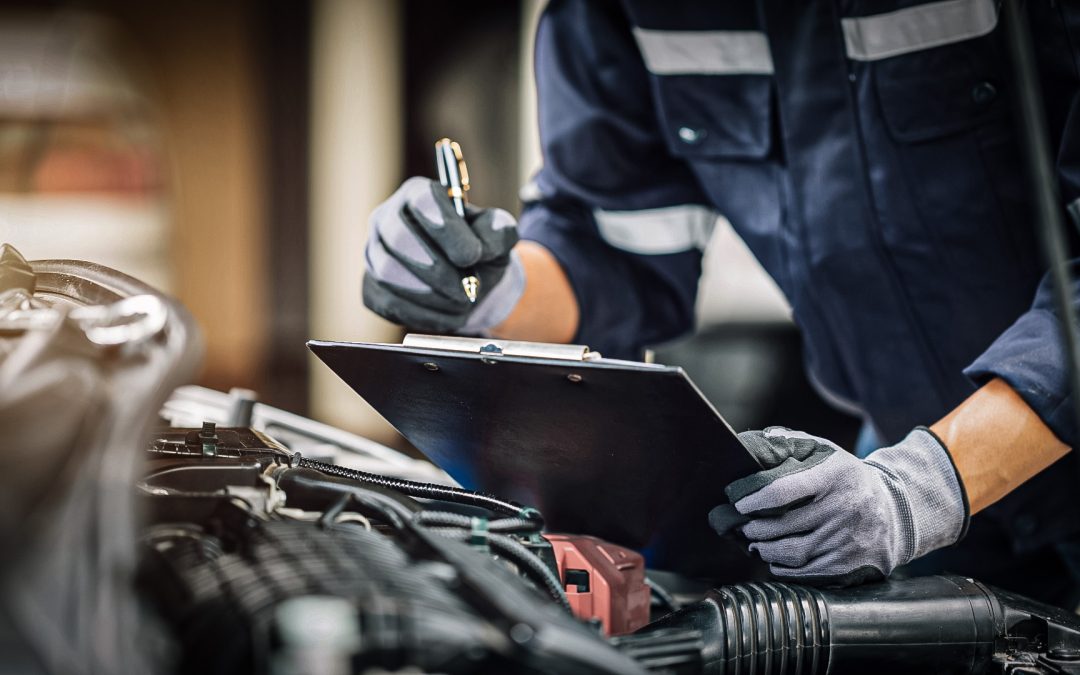
I was recently off my feet due to some unplanned surgery. Normally I go stalking around the garage like the proverbial bull in the china shop, but not lately—my ankle was a mess.
Have you ever had an injury or illness serious enough to impact the way you make a buck? I’m betting at some point in your career, it has. My daily work is no longer conventional auto repair, but it doesn’t matter much—medical maladies slow us all down in the bay, and I still spend plenty of time repairing all manner of specialty machinery. This bum leg forced me to modify how I address the repairs needed on the vehicle in my bay and how I gather the required parts for those repairs. Often we have advice here on Shop Press, but today, I suppose I’ve arrived with a question. What is the smartest way to move self and tools to and fro in the automotive service bay?
I’ve done things in the shop in the same manner for a long time, which I’ll describe in a moment, but I’m having second thoughts about whether I’ve chosen the most efficient way to plan my work. I’m also wondering if my method should have been changing over time, too.
A long time ago, I would just grab tools and work and throw things wherever I felt like. This approach was terrible for a variety of reasons, but it got worse as I got better: more involved work meant I was making bigger and bigger messes, which would have taken longer to clean up—had I actually kept up with housekeeping.
Photo: Mike Apice.
One day I was working on a vehicle and I couldn’t find the tool I needed. While not a new occurrence, this seemed to be a pretty glaring one, since I was really searching for a while. I got so frustrated that I told myself something had to change, and I quit working on the car in front of me. I cleaned my whole bay, and began anew, this time returning each and every tool to its home in the box after finishing with it. I walked a lot more, but ultimately saved time since everything was (surprisingly!) where it belonged.
And this has been my routine for about twenty years now. Much like my toolbox setup, as a mechanic, I can safely say if somethin’ isn’t broke, I don’t see a need to fix it—but perhaps I have erred.
Shortly after the impromptu cleanup mentioned earlier transpired, I wound up working as a dismantler in a salvage yard. My time was split in the bay and in my yard trucks, so I wound up piecing together a mobile box and even rigged an air compressor up on an old dentside Ford I used for heavy work when I couldn’t drag the target vehicle back to my bay.
For less involved tasks, I had a Nissan Hardbody pickup. On that, the tailgate became my mobile work area—I’d remove my toolbox from the cab and set it at the back of the bed, where I’d laid down a truck bed mat.
I had scabbed some additional bed liner material from another truck, and cut it to fit my tailgate. I screwed it in place, making a nice tool surface that kept me from laying (and leaving) my tools in the grass and gravel. It became a very handy mobile workbench or a motorized tool cart, depending on your point of view. If I took out very many parts, the gate would be a mess and I was forced into putting things away again.
That was sort of an iteration of my “work neatly at all costs” conversion, and when I came out of the yard and into a more traditional repair role, I stuck with my original system: bring one tool back to the box when you go to get another. And to be honest, it worked, so I never really brought it back for reexamination.
Photo: Mike Apice.
Until recently, that is, when my streak was punctuated for about six weeks while I was on crutches, which made work very difficult. As I improved, I was able to hobble around a bit, first with a cane and later without. Working efficiently around the shop, though, demanded some changes. Making my way to my box took some time, and I was working from my rolling stool far more than I usually did.
I began breaking things up by task and thinking several moves ahead. I’d bring a handful of tools, rags, cleaners, and chemicals over to my rolling stool, set them on the shelf, plop down, and get to work. When the task was complete, I got back up, returned all the items, and then gathered the things I’d need for the next task.
I was almost as fast as I once was. Took a little forethought on my part, but I got a surprising amount accomplished for not having use of a limb.
Now, I will admit, something crept into my head and I know most of you are already shaking your heads because you’ve probably been yelling it into your phone as you read: tool cart. A tool cart seems basically custom-made for this (and other) situations. I’ve never owned one. When I was young and broke, I just figured shoeleather was cheaper. Now that I am able to afford one, however, I feel unable to dedicate the real estate in the garage. (I know, I know. It’s really tight in there because I have a bunch of other silly tools taking up floor space that I value more highly.)
I’m in the minority here; I get it. It does seem like a cart would have been an ideal tool. Fellow Shop Press contrib Pete Meier is a diehard cart guy: “Many of the shops I worked in over the years did not assign specific bays to specific techs. Using a cart that had the tools I used the most made it easy to work where I had to without losing time running back and forth to my big box.”
I didn’t really consider that situation. I was always assigned consecutive bays, but understand why a shop would use this method, too, and I gotta say, it almost sounds like a cart is a necessity if that’s how your foreman or manager is running the show.
Photo: Mike Apice.
Especially if one has outgrown a toolbox by a bit, a cart seems great. I also see the appeal of putting some miles on the doubles of common tools we all own. Our own Greaser made an excellent point, too: “Owning a tool cart does not solve all your organizational problems. You still need to make sure to put tools back where they belong, or you’ll just have an expensive, messy box on wheels with a bunch of tools MIA. No matter how you prefer to work, or how many injured limbs you have, maintaining organization of equipment is up to you.”
And I have to wonder if I should have taken the minimalist approach, grabbed my handy road toolbox which has served me well lo these many years and pressed that back into service. Honestly, I don’t even know what I should have done, nor am I even clear on what I should do once I’m back to functioning normally, so in this instance, I’m seeking a little advice: how do you work efficiently once the car is in your bay?
The articles and other content contained on this site may contain links to third party websites. By clicking them, you consent to Dorman’s Website Use Agreement.
Participation in this forum is subject to Dorman’s Website Terms & Conditions. Please read our Comment Policy before commenting.